There is a better alternative to enameled magnet wire.
Magnet wire is used extensively in power systems for transformers and motors plus speakers, hard drives, and electromagnets – in fact anything that needs tight coils of insulated wire. “Enameled” magnet wire is misleading as it is normally copper or aluminum wire coated with a very thin layer of polymer insulation.
DTi offers effective low-cost reel to reel powder polymer coating.
Depending on what your needs are, the powder coating can impart abrasion resistance, electrical insulation, corrosion resistance, ultraviolet-light protection, non-reflection or simply decoration in a variety of colors.
We can also selectively coat parts of the material.
Our Reel to Reel Powder Coating offers some key advantages compared to conventional liquid coating techniques:
- Our process increases output, speeds production and drives down costs.
- Creates thicker coatings with no running or sagging.
- Zero or near zero VOC's (volatile organic compounds) – lowers costs.
- 95% powder utilization vs. only 40-60% for liquids – lowers costs.
- Less hazardous waste disposal vs. liquids – lowers costs.
We are experts in this technology. We use it every day for Spring-Fast®, our leading polymer-coated grommet edging brand, which protects wiring against chafe, arcing and sparking.
This coating is highly effective and as a result, is used widely in aerospace because, at 30,000 feet and close to the speed of sound, you or they don’t need wiring to chafe and cause fires. Similarly, NASCAR uses DTi's grommet edging because its mechanical attachment capability withstands the high shock and vibration that NASCAR cars face with all the bumping and crashing that is the inevitable result of high-performance cars racing around a track at 200mph.
Here is a small sample of how our coating technology has been used other than for just traditional “magnet wire”.
- Polymer-coated grommets for abrasion and corrosion resistance and retention.
- Corrosion resistance metal banding – used by utilities to hold transformers onto poles/street lights.
- “Downhole slicklines” corrosion resistance – used for tool and sample retrieval in oil drill shafts.
- Theatre wire coated with a non-reflective coating – used to avoid distracting light reflection.
- Selectively applied insulative coating on small precision metal stampings – used for mobile phone antennas.
- Steel wire ties for corrosion resistance – used for marine and exterior applications.
- Corrosion-resistant stainless steel fishing line.
Selective Coating Benefits to Electronics
Our proprietary Surface Reclamation Technology (SRT) means we can control where and how much material is applied to a substrate. The ability to create a partially coated end product is very useful to the electronics industry.
For example, various metal substrate strip materials, linear stampings, and/or bandolier electronic components, can often require both a conductive and insulative/dielectric surface. We can coat the bottom section and the sides while keeping the top section uncoated. On the bottom, you have an insulator, and on the top, you have a contact point to create a ground — typical in switch components for the electronics industry. We recently completed a selective coating job for a cell phone manufacturer that used the piece as an antenna.
Collaboration
We will work with you to meet your needs on performance and budget. We can recommend the powder formulation and roll-forming methodology. Our long experience with polymers will help guide you.
Production is tested to the ISO (International Standards Organization) inspection criteria prescribed by ASTM (American Society for Testing and Materials) standards, including crosshatch adhesion, and mandrel bend and adhesion testing.
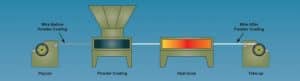
DTi's Reel to Reel Coating Process
Key Features
- Polyimide and polyester resins with thermoset or thermoplastic qualities.
- Profiles from flat wire, strip metals, precision stampings and cable and materials.
- Materials: stainless steel, aluminum and copper.
- Dimensions: from 0.010” thickness, 1.00” wide and 0.187” circumference.
- We can also fabricate, prestamp, and roll form the substrate.
If you have a need to coat wire, strip or stamped components that can run reel to reel please contact us here.